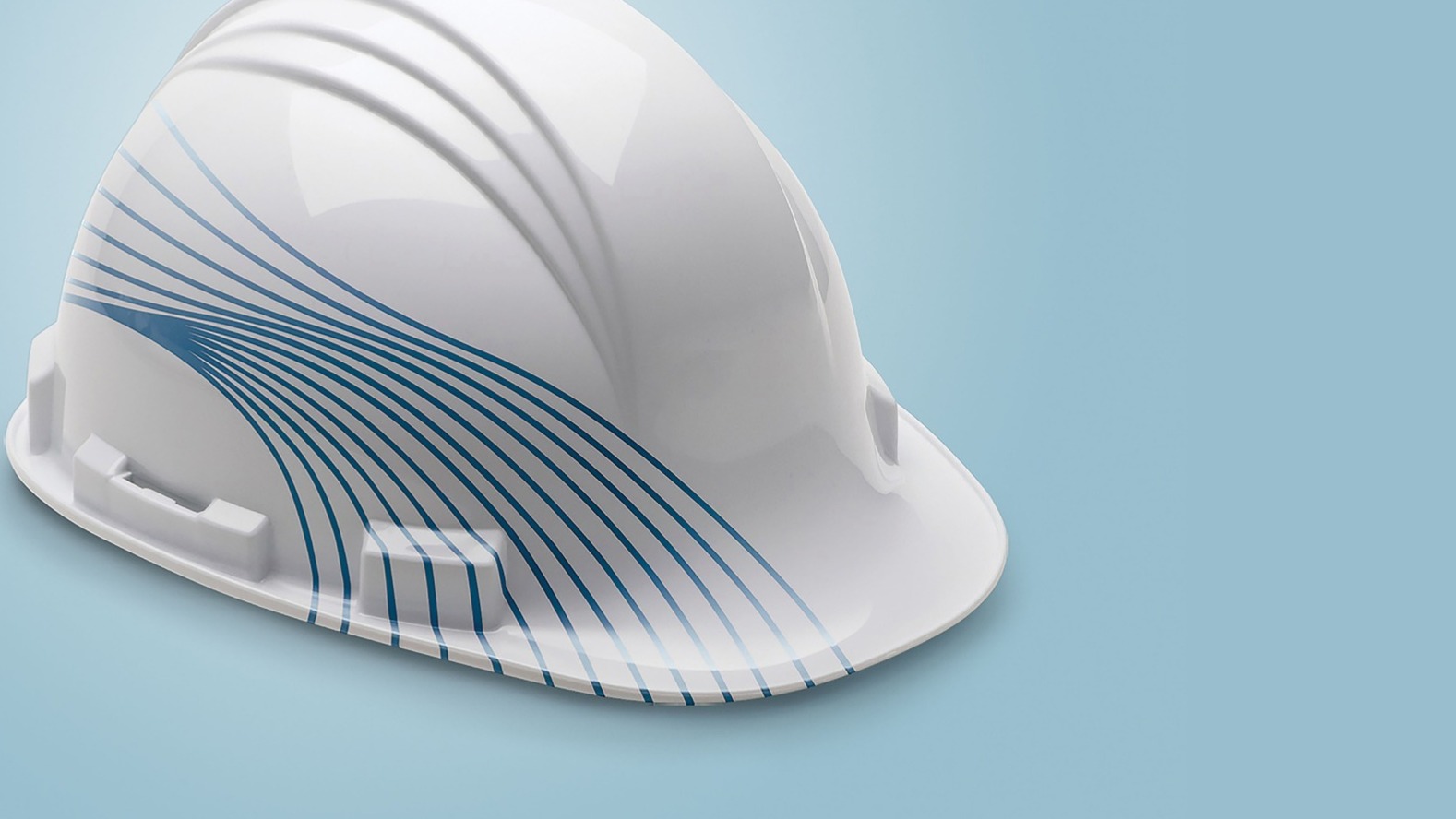
Natural Fiber Insulation Materials
Natural Fiber Insulation Materials: Manufacturing Process and Eco-Friendly Benefits
When it comes to sustainable and eco-friendly insulation options, natural fiber insulation materials have gained significant popularity. These materials offer excellent thermal performance, while also being renewable, biodegradable, and non-toxic. In this article, we will explore how natural fiber insulation materials are made, highlighting their manufacturing process and the environmental benefits they offer.
Sourcing Natural Fibers
The first step in manufacturing natural fiber insulation materials is sourcing the appropriate natural fibers. These fibers are typically derived from renewable and organic sources such as:
- Cotton: Recycled cotton fibers obtained from post-consumer textile waste or industrial scraps.
- Hemp: Fibers extracted from the hemp plant, known for its fast growth and minimal need for pesticides or herbicides.
- Flax: Derived from the flax plant, these fibers are valued for their strength and durability.
- Wool: Naturally occurring fibers obtained from sheep, providing excellent insulation properties.
- Cellulose: Made from recycled paper or wood fibers, cellulose insulation is a popular choice due to its high thermal performance.
Fiber Processing
The fiber processing stage is a crucial step in the manufacturing of natural fiber insulation materials. It involves transforming the sourced natural fibers into a form that is suitable for insulation purposes. Let's explore the fiber processing techniques commonly used in the production of natural fiber insulation materials:
Cleaning: The initial step in fiber processing is thorough cleaning. The raw natural fibers may contain impurities such as dirt, dust, and other contaminants. Cleaning ensures that these impurities are removed, resulting in clean and pure fibers. Various methods, including mechanical and chemical processes, can be employed to achieve optimal cleanliness.
Drying: Moisture content in the fibers needs to be minimized to prevent mold growth and ensure optimal insulation performance. The fibers are carefully dried to achieve the desired moisture level. This can be done using air drying techniques, low-temperature ovens, or specialized drying chambers.
Carding: Carding is a mechanical process that aligns and separates the fibers. In this step, the fibers pass through a series of fine-toothed rollers or brushes that comb and straighten them. This process helps to create a uniform and consistent texture, facilitating easier handling and installation of the insulation material.
Blending: In some cases, different types of natural fibers are blended together to enhance the insulation material's properties. Blending allows for the combination of fibers with complementary characteristics, such as strength, moisture resistance, or thermal performance. The blending process ensures a well-balanced and optimized insulation material.
Treatment: Depending on the desired performance and application, the fibers may undergo treatment processes. Treatments can include the application of fire retardants, pest repellents, or natural oils to enhance the insulation material's properties and durability. It is essential to use eco-friendly and non-toxic treatments to maintain the natural and sustainable attributes of the insulation.
The fiber processing stage plays a vital role in creating high-quality natural fiber insulation materials. It ensures that the fibers are clean, dry, aligned, and prepared for further manufacturing processes. By carefully processing the fibers, manufacturers can produce insulation materials with excellent thermal performance, moisture resistance, and environmental benefits.
Binding Agents
In some cases, binding agents are added to the natural fiber insulation materials to improve their cohesion and stability. These agents are typically eco-friendly and may include:
- Plant-Based Binders: Natural resins or oils derived from plants, such as soybean or corn-based binders.
- Mineral Binders: Inorganic substances like magnesium oxide or hydrated magnesium silicate, which provide strength and fire resistance.
The use of binding agents ensures that the natural fibers are held together in a stable form, allowing for easy installation and longevity.
Manufacturing the Insulation
After the fiber processing and binding stages, the natural fiber insulation materials are ready for manufacturing. The specific manufacturing techniques can vary depending on the desired product, such as batts, rolls, or loose-fill insulation. Common manufacturing methods include:
- Batt Manufacturing: The processed fibers are compressed and formed into large sheets or rolls, which can be easily cut and installed between framing studs or joists.
- Blown-In Insulation: Loose-fill natural fiber insulation is pneumatically blown into cavities or attics using specialized equipment, ensuring complete coverage and uniform distribution.
Environmental Benefits of Natural Fiber Insulation
Natural fiber insulation materials offer several environmental benefits, making them a sustainable choice for insulation:
- Renewable and Biodegradable: The use of organic and renewable fibers reduces dependence on non-renewable resources, minimizing the environmental impact.
- Energy Efficient Manufacturing: The production process for natural fiber insulation requires less energy compared to synthetic insulation materials, resulting in lower carbon emissions.
- Improved Indoor Air Quality: Natural fibers are non-toxic and do not release harmful volatile organic compounds (VOCs), promoting healthier indoor air quality.
- Reduced Landfill Waste: Natural fiber insulation can be easily recycled or decomposed, reducing landfill waste and contributing to a circular economy.
- Carbon Sequestration: Some natural fibers, such as hemp and flax, have the ability to sequester carbon dioxide during their growth, further mitigating greenhouse gas emissions.
Conclusion
In conclusion, natural fiber insulation materials are produced through the sourcing, processing, and manufacturing of renewable natural fibers. The eco-friendly nature of these materials, combined with their excellent thermal performance, makes them an ideal choice for environmentally conscious homeowners. By opting for natural fiber insulation, you can contribute to a more sustainable future while enjoying energy-efficient and comfortable living spaces.
Call Fargo Insulation Pros to learn more!
Frequently Asked Questions (FAQs)
Is natural fiber insulation more expensive than traditional insulation materials? Natural fiber insulation materials may have a slightly higher upfront cost, but the long-term energy savings and environmental benefits often outweigh the initial investment.
Are natural fiber insulation materials suitable for all climate zones? Yes, natural fiber insulation can be used in various climate zones. However, specific considerations may be required for extreme cold or humid regions.
Can natural fiber insulation be installed as a DIY project? While it is possible to install natural fiber insulation as a DIY project, it is recommended to consult professionals for optimal installation and performance.
Are natural fiber insulation materials resistant to pests and mold? Natural fibers like wool and cellulose have inherent properties that make them resistant to pests and mold. However, proper installation and moisture control are essential to prevent any issues.
How long does natural fiber insulation last? Natural fiber insulation materials have a lifespan comparable to other insulation types, typically lasting 40 to 50 years with proper maintenance and care.