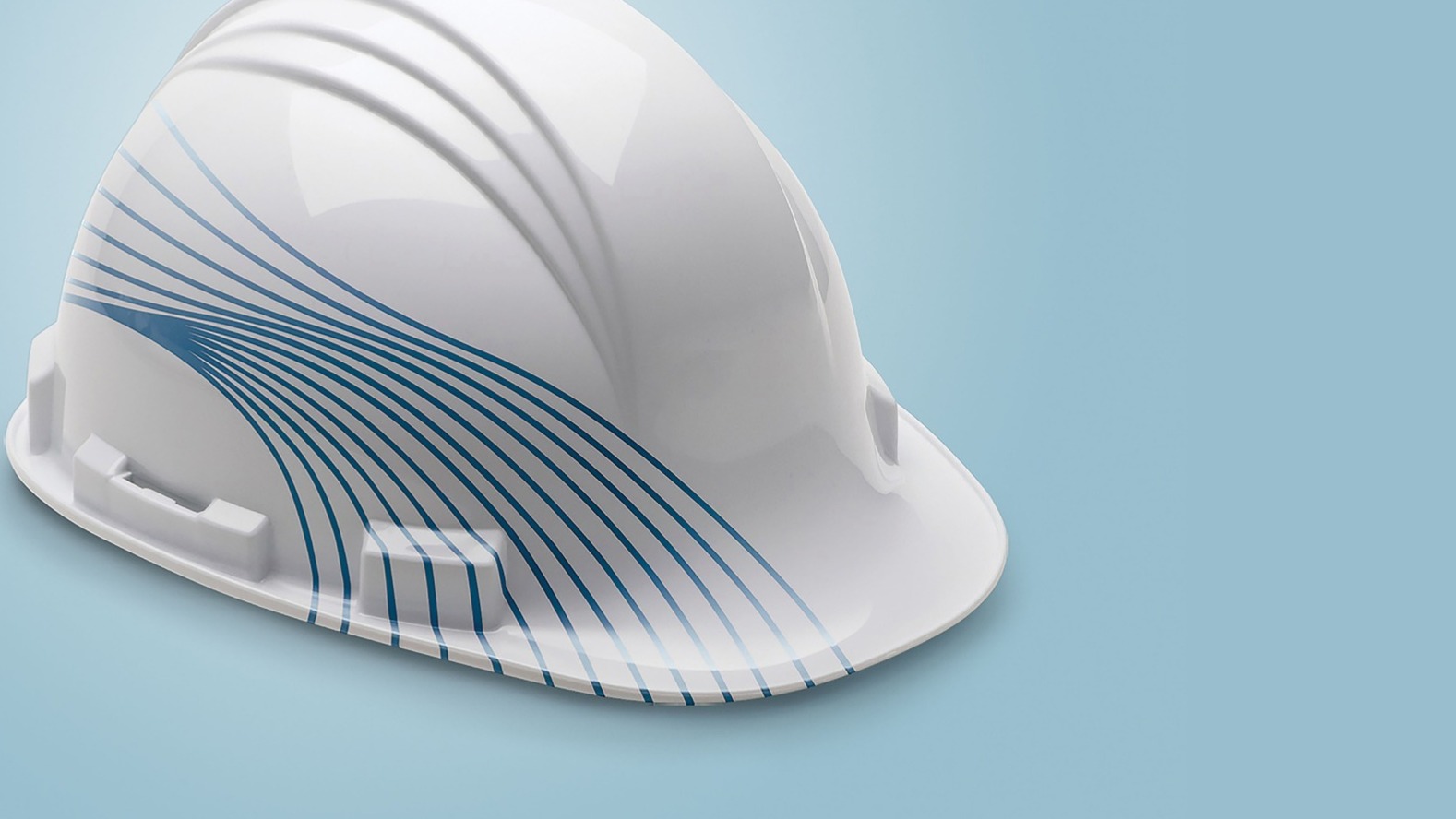
Insulation for Pipelines
Insulation for Pipelines: Maximizing Efficiency and Performance
Table of Contents
- Introduction
- Why is Insulation for Pipelines Important?
- Types of Insulation Materials for Pipelines
- Installation Methods for Pipeline Insulation
- Frequently Asked Questions (FAQs)
- Q1. Why is insulation necessary for pipelines?
- Q2. What are the common insulation materials used for pipeline insulation?
- Q3. How does insulation prevent heat loss or gain in pipelines?
- Q4. Can insulation help in preventing corrosion of pipelines?
- Q5. What factors should be considered when selecting insulation for pipelines?
- Q6. What are the installation methods for pipeline insulation?
- Conclusion
Introduction
In the world of industrial infrastructure, pipelines play a vital role in transporting fluids such as oil, gas, water, and chemicals over long distances. These pipelines are subjected to various environmental conditions, including temperature fluctuations, corrosion, and mechanical stress, which can significantly impact their performance and efficiency. This is where insulation for pipelines comes into play.
Insulation for pipelines refers to the process of applying suitable insulating materials to the external surface of pipelines. It serves multiple purposes, including thermal insulation to maintain desired fluid temperatures, protection against corrosion, reduction of heat loss or gain, and prevention of condensation. In this article, we will delve into the importance of insulation for pipelines, the types of insulation materials used, installation methods, and frequently asked questions surrounding this critical aspect of pipeline infrastructure.
Why is Insulation for Pipelines Important?
Insulating pipelines offers numerous benefits that contribute to their optimal performance and longevity. Let's explore some key reasons why insulation for pipelines is crucial:
1. Thermal Efficiency and Energy Conservation
Insulating pipelines helps to minimize heat transfer between the fluid inside and the surrounding environment. By reducing heat loss or gain, insulation ensures that the fluid maintains its desired temperature, leading to improved thermal efficiency. This results in energy conservation and cost savings by reducing the need for additional heating or cooling.
2. Condensation Prevention
When pipelines carry fluids at temperatures lower than the ambient air, condensation can occur on the outer surface of the pipe. This moisture accumulation can lead to corrosion and damage to the pipeline infrastructure. Insulation acts as a barrier, preventing the formation of condensation and safeguarding the integrity of the pipeline.
3. Corrosion Protection
Pipelines are susceptible to corrosion caused by exposure to moisture, chemicals, and other external factors. Insulation acts as a protective layer, shielding the pipeline from these corrosive elements and extending its lifespan. It also reduces the likelihood of leaks and breakdowns, enhancing the overall safety of the infrastructure.
4. Environmental Considerations
Insulating pipelines aligns with environmental sustainability goals. By reducing energy consumption and heat emissions, insulation contributes to a smaller carbon footprint. This is particularly important in industries where significant amounts of energy are required for fluid transportation.
Types of Insulation Materials for Pipelines
Various insulation materials are used for pipelines, each with its unique properties and applications. Let's explore some common types of insulation materials utilized in pipeline insulation:
1. Polyurethane Foam Insulation
Polyurethane foam insulation is a popular choice for pipeline insulation due to its excellent thermal properties and versatility. It is applied as a spray or injection foam, creating a seamless and uniform insulation layer. Polyurethane foam insulation provides high thermal resistance and is resistant to moisture and corrosion.
2. Fiberglass Insulation
Fiberglass insulation consists of glass fibers bound together with a resin. It is available in the form of pre-formed sections or loose-fill insulation. Fiberglass insulation is known for its low thermal conductivity, making it an effective choice for reducing heat transfer in pipelines.
3. Mineral Wool Insulation
Mineral wool insulation is produced by melting and spinning natural or manufactured into fibers. It is available in various forms, including blankets, boards, and loose-fill insulation. Mineral wool insulation offers excellent thermal and acoustic properties, as well as resistance to fire and high temperatures.
4. Cellular Glass Insulation
Cellular glass insulation is made from crushed glass combined with a foaming agent. It is produced in rigid board form and is known for its exceptional thermal insulation properties, resistance to moisture absorption, and fire resistance. Cellular glass insulation is commonly used for cryogenic and low-temperature applications.
Installation Methods for Pipeline Insulation
Insulating pipelines requires careful planning and proper installation techniques to ensure effective and long-lasting insulation. Let's explore two common installation methods used for pipeline insulation:
1. Field-Applied Insulation
Field-applied insulation involves installing insulation materials on-site directly onto the pipelines. This method allows for customized insulation solutions, as the insulation material can be adjusted according to specific pipeline requirements. Field-applied insulation is commonly used when dealing with complex pipeline systems and irregular shapes.
2. Pre-Insulated Pipe Systems
Pre-insulated pipe systems involve factory-made pipes with insulation already applied during the manufacturing process. These pre-insulated pipes come in various configurations, such as single or dual pipes with insulation sandwiched between them. Pre-insulated pipe systems offer faster installation and consistent insulation quality.
It is essential to consult with insulation experts and adhere to industry best practices when selecting the appropriate insulation material and installation method for pipeline insulation. This ensures optimal performance, durability, and compliance with regulatory standards.
Frequently Asked Questions (FAQs)
Q1. Why is insulation necessary for pipelines?
Insulation for pipelines is necessary to maintain desired fluid temperatures, protect against corrosion, conserve energy, and prevent condensation.
Q2. What are the common insulation materials used for pipeline insulation?
Common insulation materials for pipeline insulation include polyurethane foam, fiberglass, mineral wool, and cellular glass insulation.
Q3. How does insulation prevent heat loss or gain in pipelines?
Insulation materials have low thermal conductivity, reducing heat transfer between the fluid inside the pipeline and the surrounding environment.
Q4. Can insulation help in preventing corrosion of pipelines?
Yes, insulation acts as a protective barrier against corrosive elements, extending the lifespan of pipelines and reducing the likelihood of leaks.
Q5. What factors should be considered when selecting insulation for pipelines?
Factors such as temperature requirements, environmental conditions, corrosion resistance, and regulatory compliance should be considered when selecting insulation for pipelines.
Q6. What are the installation methods for pipeline insulation?
Common installation methods include field-applied insulation, where insulation materials are installed on-site, and pre-insulated pipe systems, which come with insulation already applied during manufacturing.
Conclusion
Insulation for pipelines is a crucial aspect of maintaining efficient and reliable fluid transportation infrastructure. By considering the thermal, corrosion, and environmental factors, pipeline insulation provides numerous benefits such as energy conservation, condensation prevention, and corrosion protection. Selecting the appropriate insulation material and installation method, in adherence to industry standards, ensures optimal performance and longevity of pipelines.
Insulating pipelines not only enhances their efficiency and durability but also contributes to a more sustainable and environmentally friendly operation. It is imperative to consult with insulation experts and professionals to determine the best insulation solutions for specific pipeline requirements